Tolerances
Tolerances vary depending on part feature such as bends, offsets, holes and inserted hardware. The following tolerances will be guaranteed by China Manufacturing Corp. for precision sheet metal fabrications. Our standard angular tolerance is +/- 1 degree and we hold a fractional tolerance of +/- 1/64 in.
Locational Tolerances |
Tolerances on One Surface |
Bend to bend (2 bends) |
+/- 0.015 in. |
Bend to bend (3 or more bends) |
+/- 0.030 in.* |
Edge to hole (2 bends) |
+/- 0.015 in. |
Bend to hole (2 bends) |
+/- 0.030 in.* |
Bend to hole (3 or more bends) |
+/- 0.030 in.* |
Hole to formed feature or hardware |
+/- 0.010 in. |
Hole to formed feature or hardware (2 or more bends) |
+/- 0.030 in.* |
Edge to formed feature or hardware |
+/- 0.010 in. |
Edge to formed feature or hardware (2 or more bends) |
+/- 0.030 in.* |
Hole to hole (2 or more bends) |
+/- 0.020 in.* |
Edge to edge (2 or more bends) |
+/- 0.020 in.* |
Edge to bend (more than 1 bend) |
+/- 0.020 in.* |
|
Edge to edge |
+/- 0.005 in. |
Edge to hole |
+/- 0.005 in. |
Hole to hole |
+/- 0.005 in. |
Hole to hardware* |
+/- 0.010 in. |
Edge to hardware* |
+/- 0.010 in. |
Hardware to hardware |
+/- 0.015 in. |
Bend to edge |
+/- 0.010 in. |
Hole Tolerances
Hole diameters |
+/- 0.005 in. |
Hardware hole diameters |
+/- 0.003 in. |
Countersink major diameters |
+/- 0.005 in. |
Countersink minor diameters |
+/- 0.015 in |
|
*non cumulative
Surface Finishes for Sheet Metal
Typically, we break (deburr) the edges of all sheet metal fabricated parts. In some instances your project may require additional finishes.
Mill Finish |
Orbital Sanding |
Edge Breaking |
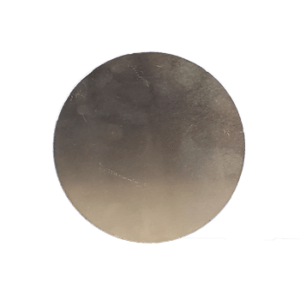 |
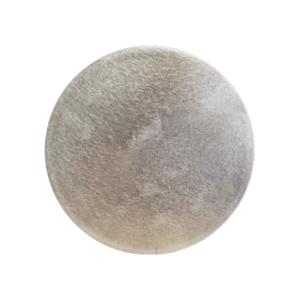 |
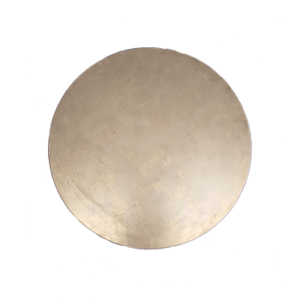 |
A variety of powder coat paint colors are available in textured and non-textured finishes, including RAL colors. Silk screening is also available up to two colors and can be matched to any Pantone number.
Part Marking
We offer two methods of part marking: ink stencil and bag and tag. Ink stencil is a method in which we spray a permanent ink over a stencil to create the marking. Bag and tag is when parts are wrapped and labelled with part number sticker.
Welding
China Manufacturing Corp. offers the following single component welding methods: seam, stitch, and tack.
Seam Weld
Seam welding is simply a continuous weld along a joint and is typically the strongest welding method because it completely welds a joint. The main advantage of seam welding is the strength and durability of the weld. A common application for seam welding is in the corners of a folded-up sheet metal chassis. Seam welding the corners gives the appearance of a solid box and makes the chassis stronger. Other applications include brackets for load bearing, areas where there can be no gaps for contaminants to enter, and frame components that will be load bearing.
Stitch Weld
Stitch welding is a weld along a joint that is broken up into equal length and equal spaced welds, giving the weld a stitched look. Stitch welding reduces the amount of heat distortion and also is less costly than a full seam weld. Stitch welding is typically used when the strength or look of a seam weld is not needed.
Tack Weld
Tack welding is the use of small strategically placed beads of weld typically used to secure parts in place before final welding. Tack welding allows the parts or assembly to be adjusted and properly fitted for the final weld to take place. Tack weld can be used to weld where a spot welder cannot reach, for example in long chassis or metal boxes.
Seam Weld |
Stitch Weld |
Tack Weld |
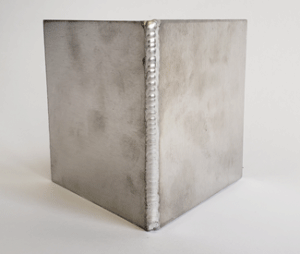 |
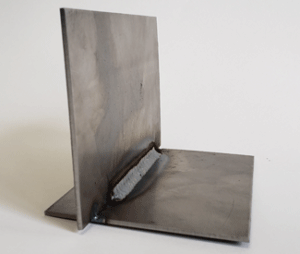 |
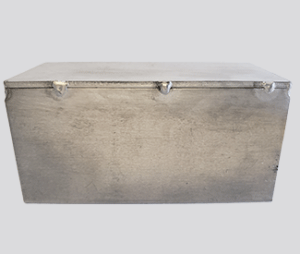 |
Assembly
We will ship loose components or provide POP riveting up to four components.
Tip: If you have more than four components, we can fabricate them and ship them loose.
FOR A FULL LIST OF FINISHING CAPABILITIES>
Documentation
The following documentation is available for all sheet metal orders; ISO9001, a certificate of conformance, and material certifications are available upon request.